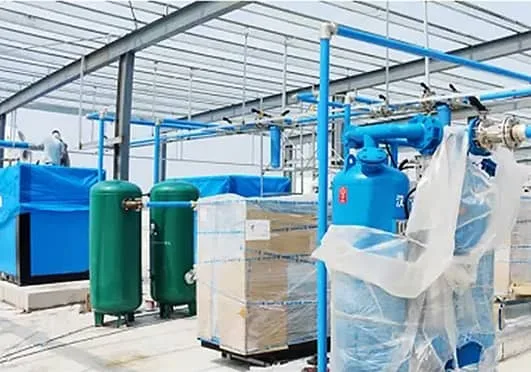
How to Control the Leakage of Compressed Air Within a Reasonable Range?
Compressed air is one of the most widely used power sources in the industrial field. Because of its many advantages such as safety, pollution-free, good adjustment performance, and convenient transportation, it is widely used in the field of modernization and automatic power.
However, compressed air is also an expensive source of energy. Continuously reducing the overall operating cost of compressed air is an important issue for every factory manager. Compressed air leaks are one of the most common types of energy waste in factories, accounting for an average of 30% of the total compressed air consumption—this results in significant electricity losses every year.
Common Sources of Air Leaks
Leaks usually occur in the following locations:
- Pipe joints and quick-connect couplings
- Pressure regulators (FRL units)
- Frequently opened condensate drain valves
- Cracked hoses or broken pipes
Leakage Rates by System Age and Size
It is nearly impossible to completely eliminate air leaks. What we can do is control them within a reasonable range:
- New systems or small factories: 5% – 7%
- 2–5 year-old systems or medium factories: 7% – 10%
- Older than 10 years or large factories: 10% – 12%
Impact of Leaks
Leaks not only directly waste energy but also lead to indirect losses. As leaks increase, system pressure drops, which may trigger additional compressors to maintain pressure—further raising electricity costs. Intermittent discharge devices (e.g., blow down valves) can also cause sudden pressure drops, potentially leading to system shutdowns.
Three Methods to Quantitatively Evaluate Compressed Air Leakage
1. Air Storage Volume Measurement
Assuming the air system is airtight except for leaks, use the following formula:
Qleak = (ΔP / P0) × (V / T)
Where:
Qleak: Leakage (m³/min)
ΔP: Pressure drop (bar)
P0: Absolute pressure (bar)
V: Volume of air storage (m³)
T: Time (min)
2. Compressor Operation Test
Turn off all equipment and monitor the compressor running in On-Line/Off-Line mode:
Qleak = Q × (T / (T + t))
Where:
Q: Compressor displacement (m³/min)
T: Loading runtime (min)
t: Unloading runtime (min)
3. Ultrasonic Leak Inspection
This method detects high-frequency sound generated by leaks. Ultrasonic leak detectors typically include a microphone, filter, display, and headphones. Detection steps include:
- Inspect the factory for obvious leaks
- Use a test gun along the air lines while adjusting sensitivity
- Start from the compressor and move downstream
- Subdivide the detection area for systematic coverage
- Label each detected leak for follow-up repair
- Recheck the system after repairs
- Calculate leakage amount
- Compile a leak detection report
In practice, it is recommended to combine methods 1 and 2 for a total leakage estimate, and method 3 for identifying specific leak points.